Chairman Morihiro Saito (This is how a world-famous invention was born)
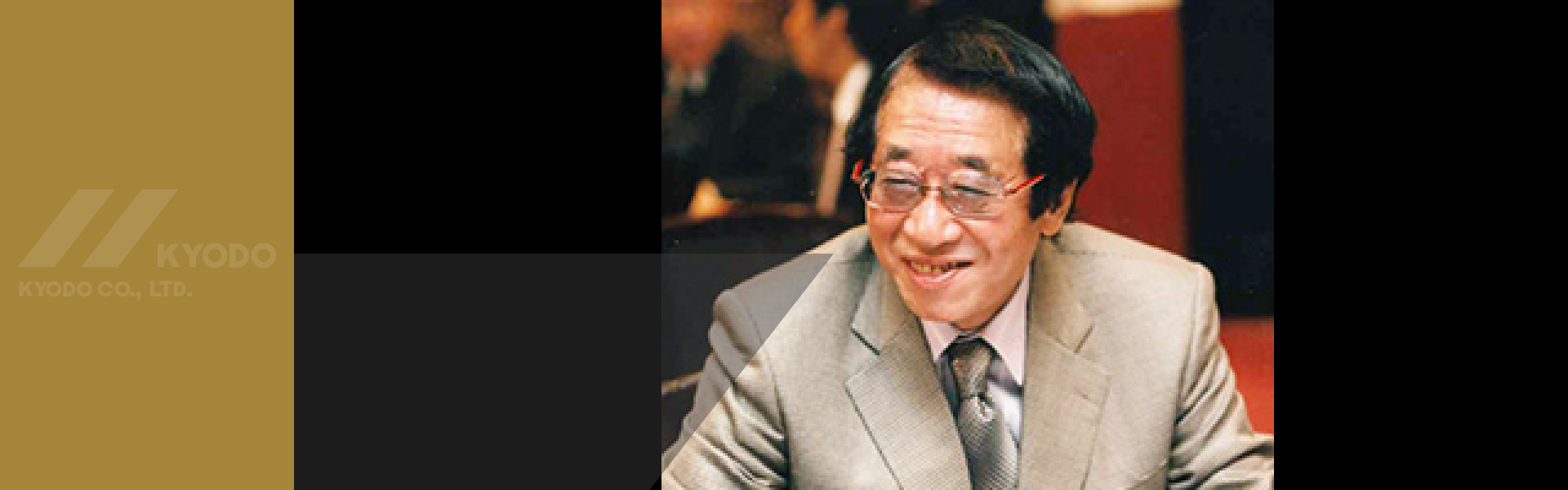
Morihiro graduated from Gakushuin University in 1965. After graduating from Gakushuin University in 1965, Morihiro worked for about four years at Okayama Rubber Kogyo Co.
This is how a world-class invention was born
It started with a simple word
The development of the rubber bushing began during my apprenticeship at Okayama Rubber Company when a customer of an agricultural and forestry equipment manufacturer, who I was in charge of sales for, muttered to me, "I wonder if there is anything cheaper and easier to handle for the bearings in brushcutter tubes. It was a casual remark.
Brushcutters are used in a variety of ways.
A brushcutter is equipped with a 1,500mm-long &phi. 7mm (or &phi. 7mm) bearing inside an aluminum pipe (outer tube) to transmit the rotation of the engine to the blade at the tip; The drive shaft is made of stainless steel and is connected to the gear case at the end of the drive shaft. The "rubber bushing", which is a metal sleeve covered with rubber, plays a role in suppressing the runout of the driveshaft, which turns nearly 10,000 rpm. Normally, five rubber bushings are installed in one brushcutter.
That know-how produced a bestseller
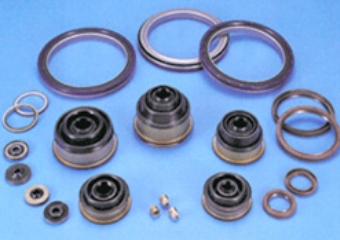
Until rubber bushings were introduced to the market, expensive needle bearings were used, but with the introduction of these rubber bushings developed by Morihiro, the cost was reduced by less than half.
At that time, our company was using oil bearings.
At that time, our company had an affiliated rubber manufacturer manufacture oil seals on consignment and marketed them under the trademark "KYODO OIL SEAL. Oil seals are used in a variety of fields as bearings for rotating shafts, especially in sealing lubricating oil used in rotating parts and preventing the entry of foreign substances. The rubber used must also withstand prolonged use, so excellent oil resistance is required.
Industrial rubber materials are completed as production materials by each rubber manufacturer by blending about 50% of basic raw materials purchased from JSR (former Nippon Synthetic Rubber Co., Ltd.) or ZEON Corporation with several chemicals based on its own know-how. In this respect, compared to plastic materials, which are purchased from material manufacturers by specifying the product name and number, rubber is a delicate material that is extremely difficult and time-consuming to handle.
Also, even if rubber is made according to the drawing at the time of molding, it may shrink or swell during use. Therefore, if the purpose, environment, and conditions under which the rubber parts will be used are not carefully understood before mixing the materials, problems may occur months or even years after the rubber parts are used in the market. In particular, oil seal manufacturers, which are critical components, must be proven and trusted companies.
In this way, the rubber know-how that our company has built up in the field of oil seals is the basis for the invention of the rubber bushing by Morihiro.
What supported this passion
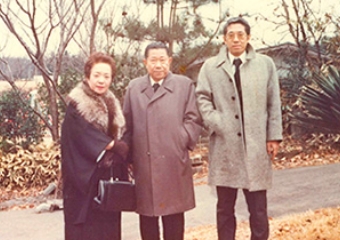
Now, after completing his training at Okayama Rubber Company and joining our company, Morihiro had a vivid image in his mind of that customer's words.
"I have been using a brushcutter for a long time.
"A professional would use a brushcutter for two or three years. I wonder if the bearings used in brushcutters as a matter of course nowadays are not actually over-specified. There must be a better way to do it. I'm a rubber maker. Okay, let's give it a try." It was a good day when the idea came to him, and he was 28 years old.
The basic concept was to use a copper bearing with low frictional resistance as the drive shaft bearing, and to cover the copper bush with rubber to absorb vibration. Also, the bearings up to now had such high dimensional accuracy that it took a lot of nerve to press-fit five bearings in position in the aluminum pipe. Even so, it took Morihiro, who did not have sufficient technical knowledge at the time, a year to arrive at this basic concept.
"I never miss a fortune or turning point in my life. I was a law school graduate and certainly didn't know much about machines, but the various experiences I had gained as an outlaw would surely produce ideas that would astonish everyone around me." The young Morihiro never gave up believing so.
It was also a big help that Mrs. Morihiro's parents were a family of engineers, and her father-in-law, a graduate of the College of Science and Engineering at Nihon University, gave her technical advice on machinery and design.
Morihiro says, "I think there are many ambiguous parts in economics and law, but in that respect, machines are simply 1 + 1 = 2 and there is only one answer. And for me, the more I studied, the more I got into my head." He looks back.
For the material of the bushing, he took his father-in-law's advice and selected brass, which has low frictional resistance, and purchased a round brass pipe bar from a secondary wholesaler. For the rubber material that encases the bushing, we selected NBR, which has excellent oil resistance, and press-fitted it into the bushing with an inner diameter 0.5 mm smaller than that of the bushing. The rubber sheets for the prototype were procured from Yamazaki Rubber & Chemicals, a company that Chairman Emeritus Zou Hayashi had founded with him when he was a junior high school student and that Morihiro had been "forced" to work part-time for 10 days by Chairman Hayashi. He was very generous with his cooperation in mixing the rubber sheets for the prototype.
In making the drawings, "My drawing skills were still rudimentary, but the design techniques my father-in-law taught me and my young ability to learn anything at this time became the starting point, and I drew the drawings myself using a drifter." That is right. And in the product column of the drawings that Morihiro himself drew up, he put the words "rubber bushing.
What is the meaning of our existence
The people who helped us evaluate and test the prototype were from the engineering department of Fuji Motors, the predecessor of the current Husqvarna Zenoah Corporation, which has been a customer of our company since its establishment and with whom we have been in business for over 70 years. During the two years of repeated trial and error, they sensed Morihiro's passion and kindly lent their help. Finally, after three years of hard work, the rubber bushing was completed. This was the moment when Morihiro, 31 years old, took a big step forward as a sales section manager.
"Why didn't you file a patent?" "Why didn't you patent it?"
"Nearly 40 years have passed since then, and the Rubber Bush is now used all over the world as a matter of course. We thought that the industry would grow and our company would benefit if everyone in the world used these patents, not just us. He answered in a friendly manner.
Chairman Morihiro Saito concluded.
"We need to have the spirit to bounce back from any adversity. And effort, effort, effort. Everyone will get a chance at some point. When you feel it, you just have to go for it."
It is true that components such as rubber bushings are not so visible to the public and are not glamorous products. Even so, I was reminded that the curiosity to pick up on the casual comments of customers, the passion to create them at any cost, and the technical capabilities that support research and development create "good parts," and that each of these parts crystallizes into a "good product.
There were hints hidden in our history as to what kind of existence our company "Kyodo" should have for society.
I found the hint in our history.
- Ignite
- Chairman Morihiro Saito (This is how a world-famous invention was born)
- Hiroshi Saito, President and Representative Director
- Takeshi Saito, Representative Director, Vice President
- Kento Urata, Sales Department, Section Chief,
- Naoaki Kouketsu, Quality Assurance Dept.
- Teppei Kamagata, Chief, Technical Development Dept.
- Kazuki Moriyama, Sales Department Section Chief
- Yujiro Oohira, Sales Department Section Chief
- Kyousei Naya, Sales Department Section Chief
- Koichi Hirano, General Manager, New Business Division
- Kyodo Asian ・ General Manager Asian Tiger (tentative)
- Kyodo Asian ・ General Manager Asian Tiger (tentative)
- Kyodo Asian ・ General Manager Asian Tiger (tentative)